
“Pigs were constructed of open cell polyurethane foam with various densities. “In order to be prepared for any cleaning contingency, we provided 18 pigs for the project,” said Murphey. Rex Murphey, Montauk Services CEO, explained the actual pigging operations.
#Galcon construction manual
“In addition, we had to construct the launcher and support system, pour a concrete reinforcing pad for the launcher, manage the pumping operations, facilitate the pig launching and retrieval, coordinate site revetment, construct a display for the launcher, ensure the system could handle the pressure requirements of the operation, and produce a pigging manual for future reference.” “This was a large undertaking and very unconventional,” he said. This forced us to run three 18-inch HDPE lines across the main road for the island, resulting in having to construct a highway-rated, temporary bridge to allow continued roadway access.” (The lines couldn’t be buried due to underground utilities.)
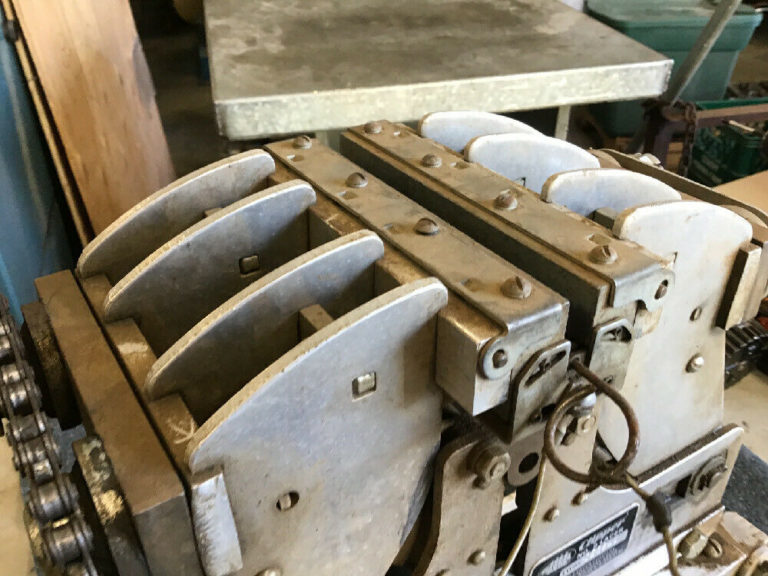
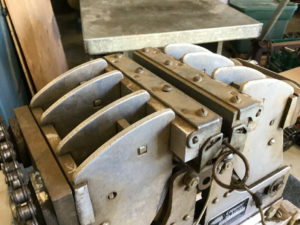
The water used to push the pigs through the line had to come from the inner lagoon. “Using smaller gear for retrieval, proper planning, outside-the-box thinking and lots of luck from the weatherman,” Vogt continued, “we were able to launch and retrieve pigs in a higher sea state. But from a marine standpoint, the prevailing winds at that time of year are predominantly from a bad direction, making the retrieval of pigs, ROV operations and drawing water for the operation very difficult.

Vogt said the time frame chosen was good for the city because it was the lowest usage interval for its clients.
#Galcon construction full
“The two largest challenges,” said Ryan Vogt, project manager with Galcon Marine, “were completing the project within the allocated time frame, due to poor weather conditions, and constructability of the project, which required maintaining full access on the island for resident and emergency vehicles.” However, weather was expected to be even worse later in the winter, and could affect all work operations, particularly the pumped water delivery necessary to propel pigs through the intake lines. 15, 2018, even though weather conditions during that time of year could complicate marine operations. The project scope of work specified that pipe cleaning had to be accomplished between Oct. Montauk Services was designated as the pigging contractor, Associated Engineering was the engineering consultant and Bennet Mechanical constructed the pig launcher. Galcon Marine, the general contractor, developed and executed a plan for cleaning the intake lines and provided complicated marine logistics and construction support. This approach placed the project risk and the methodologies into the hands of those best-informed and best-equipped to plan and execute it, reducing the city’s exposure and making project delivery efficient. The owner, City of Toronto, tendered the project as a design-build contract due to limited regional pipe-cleaning expertise, said Niall Robertson, Island Water Treatment Plant manager. This involved inserting and propelling a device, or “pig,” to scrape and clear the pipe interior. Quagga mussels have spread from Eastern Europe to the United Kingdom and now have invaded North American waters.įlow test results prompted the city to initiate planning to clean all three intakes via hydraulic pigging. They also can disrupt natural ecosystems by facilitating the growth of nuisance weeds along the bottom of lakes and rivers.
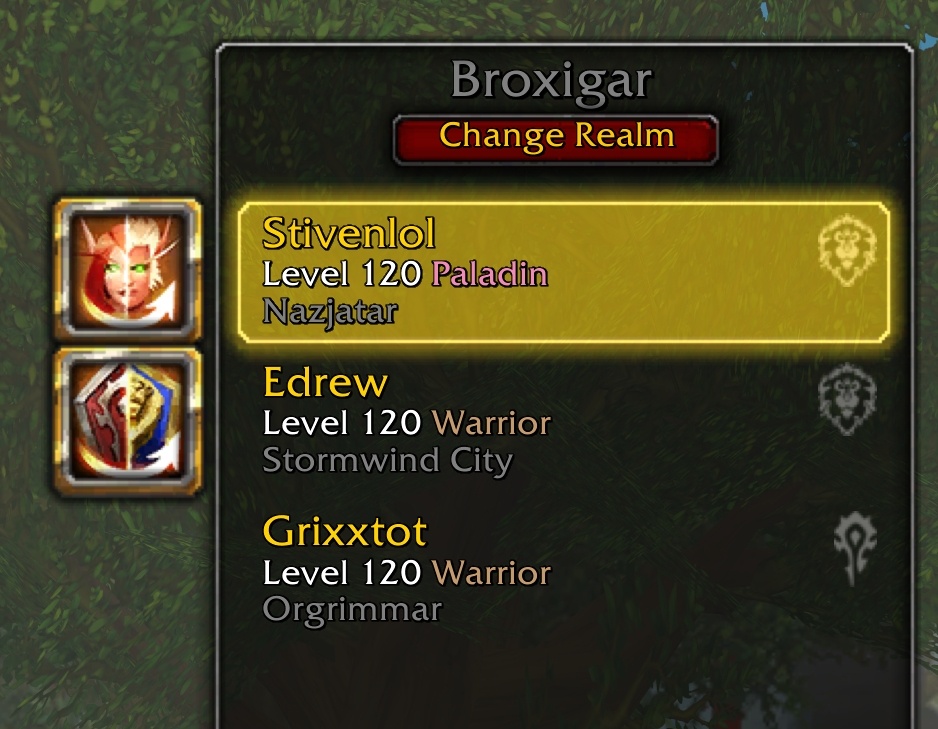
Small quagga mussels breed rapidly, and quickly clog pipe inlets or outlets, ultimately requiring physical removal. The inspection confirmed that the accumulation of mussels had significantly reduced water flow from the lake into the treatment plant. The project was initiated after an underwater inspection in 2014 conducted by a remotely operated vehicle (ROV) verified the presence of quagga mussels throughout the entire length of each intake line. Mouths of the pipes are approximately 270 feet below the lake’s surface and run along the natural slope of the lake bottom, following the near-shore embankment and contained on the lake floor by concrete anchor blocks, comprised of 9,550 cubic yards of concrete. The DLWC system operates 24 hours a day, 365 days a year. One of four serving Toronto, the Island treatment plant provides the sole supply of the city’s deep lake water cooling (DLWC) partnership with Enwave Energy Corporation.
